Directives d'inspection et de maintenance des robots photovoltaïques de type rail
La première inspection du robot photovoltaïque sur rail doit être effectuée immédiatement après l'installation afin de garantir le bon fonctionnement de tous les systèmes. Les cycles d'inspection de routine ultérieurs peuvent être ajustés en fonction des situations et des besoins spécifiques ; cependant, les recommandations suivantes sont généralement recommandées :
- Inspection initiale:Effectué immédiatement après l'installation.
- Inspection quotidienne:Effectué une fois par jour pour assurer le fonctionnement normal des systèmes du robot.
- Inspection d'entretien hebdomadaire:Effectué une fois par semaine pour une maintenance et des inspections complètes afin de garantir la stabilité et la fiabilité à long terme de l'équipement.
- Inspection trimestrielle:Réalisée tous les trois mois, en se concentrant sur les composants clés et les fonctions du système pour assurer le fonctionnement dans différentes conditions environnementales saisonnières.
- Inspection annuelle:Effectué une fois par an pour une évaluation complète des performances et des réparations nécessaires, garantissant la fiabilité et la sécurité pour un fonctionnement à long terme.
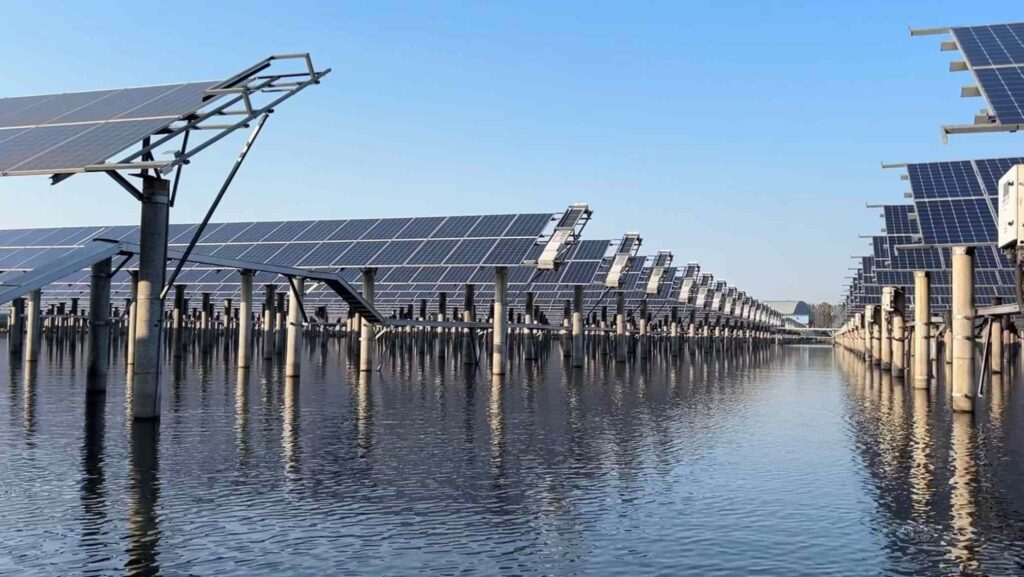
Équipement de nettoyage de panneaux solaires Inspections quotidiennes
- Vérifications des fonctions de base
- Vérifiez que tous les capteurs (par exemple, les capteurs de température, d’humidité, de gaz) fonctionnent correctement.
- Vérifiez la puissance du signal du module de communication pour garantir une transmission de données stable.
- Vérifiez la fonctionnalité de charge automatique pour vous assurer que le robot peut retourner avec succès à la station de charge.
- Contrôles d'adaptabilité environnementale
- Inspectez les capacités du robot en matière de résistance à la poussière, à l’eau et à l’humidité.
- Confirmer le fonctionnement du robot dans des conditions de température élevée et basse.
- Exécution des tâches d'inspection
- Assurez-vous que le robot effectue des inspections automatiques le long des chemins prédéfinis et des cibles d'inspection.
- Vérifiez la capacité de l'opérateur à effectuer des tâches d'inspection via la télécommande.
Inspections hebdomadaires
- Maintenance du système
- Nettoyez la surface du robot en éliminant la poussière et la saleté.
- Inspectez les composants mécaniques du robot, tels que les roues motrices, les roues de support et les roues de guidage, pour vous assurer qu'il n'y a pas d'usure ou de dommage.
- Vérifiez que la prise de charge automatique et la fiche sont correctement en contact.
- Mettez à jour le système logiciel du robot pour garantir son fonctionnement avec la dernière version.
- Tests de fonction
- Retestez les fonctions de surveillance d'imagerie du robot pour garantir la stabilité des caméras HD et des dispositifs d'imagerie thermique infrarouge.
- Vérifiez les fonctionnalités d’alarme/avertissement incendie pour vous assurer que les capteurs et les algorithmes fonctionnent normalement.
- Vérifiez les fonctions de lecture des compteurs pour garantir des lectures précises des différentes données des instruments.
- Inspectez la fonctionnalité de l'interphone vocal pour assurer une communication fluide entre le personnel et le robot.
Inspections trimestrielles
- Vérifications des composants clés
- Inspectez en détail les dispositifs d’entraînement, les dispositifs d’alimentation et les dispositifs de détection pour vous assurer qu’il n’y a pas de panne.
- Examinez l’état d’usure des chenilles et remplacez-les ou réparez-les si nécessaire.
- Vérifiez la sensibilité et la précision des capteurs et calibrez-les si nécessaire.
- Tests d'adaptabilité environnementale
- Effectuer des inspections dans diverses conditions météorologiques (par exemple, ensoleillé, pluvieux, neigeux) pour valider l'adaptabilité environnementale du robot.
- Vérifiez la capacité d'escalade et la profondeur de pataugeoire du robot pour vous assurer qu'il fonctionne normalement sur un terrain complexe.
- Gestion des données
- Examinez la stabilité et la fiabilité de la transmission des données pour garantir que les données d’inspection peuvent être téléchargées rapidement vers le système de surveillance principal.
- Vérifiez les fonctionnalités du système de gestion des données pour garantir un stockage, une analyse et une génération de rapports précis.
Inspections annuelles
- Évaluation complète des performances
- Évaluez les performances globales du robot, y compris les performances mécaniques, électriques et logicielles.
- Vérifiez la durée de vie du robot et évaluez l'état d'usure des différents composants, en les remplaçant si nécessaire.
- Examinez les performances de sécurité du robot pour garantir un fonctionnement sûr dans divers environnements extrêmes.
- Optimisation du système
- Optimisez les chemins et les fréquences d'inspection du robot en fonction des données d'exploitation d'un an.
- Examinez les enregistrements de défaillance du robot, analysez les causes courantes de défaillance et proposez des mesures d’amélioration.
- Mettre à jour les algorithmes et les logiciels du robot pour améliorer la précision et l'efficacité des inspections.
- Manuels de formation et d'exploitation
- Former les opérateurs pour s’assurer qu’ils connaissent les dernières fonctionnalités et méthodes opérationnelles du robot.
- Mettre à jour le manuel d’utilisation pour garantir qu’il reflète les fonctionnalités et les processus opérationnels actuels du robot.
En suivant ces dispositions détaillées du cycle d'inspection, nous pouvons garantir que le robot photovoltaïque de type rail reste dans un état de fonctionnement optimal, fournissant un support technique fiable pour les travaux d'inspection des centrales photovoltaïques.